Uczestnicząc w procesach informatyzacji produkcji u naszych klientów niejednokrotnie spotykamy się z potrzebą informatyzacji działu planowania produkcji. W zasadzie bez znaczenia czy jest to małe przedsiębiorstwo czy organizacja bardziej złożona np. z kilkuset i więcej pracowników czy też kilku zakładów produkcyjnych. Mimo wykorzystywanych przez te przedsiębiorstwa systemów klasy ERP działy planowania produkcji najczęściej i tak korzystają z Arkuszy Microsoft Excel.
Dzieje się tak zazwyczaj z kilku względów, jak brak dostatecznych funkcjonalności systemu ERP, brak możliwości uwzględnienia w systemie szeregu zmiennych, wyjątków etc. Narzędzie Excel okazuje się bardziej elastyczne względem systemu i wbrew pozorom dające więcej możliwości. Z czasem jednak staje się coraz bardziej uciążliwe, chociażby z uwagi na czas jaki musi poświęcić planista na opracowanie planu lub dokonanie jego modyfikacji. Kiedy pojawia się już tzw. zielone światło czy wręcz konkretny budżet na wprowadzenie systemu typu APS pojawiają się schody.
By móc skorzystać z dobrodziejstwa systemu APS konieczne są dobrej jakości dane wejściowe.
Mowa tu o parametrach parku maszynowego jak wydajności, dostępności, powiązanie produktu/operacji z maszyną, wskazanie maszyny alternatywnej etc. Kolejnym istotnym elementem wykorzystywanym przez APS jest macierz przezbrojeń, którą należy zdefiniować. Jednakże podstawowymi danymi wejściowymi, a które wbrew pozorom najczęściej przysparzają nie mało problemów jest technologia produkcji. Zastanawiające? No tak MRP także wykorzystuje przecież technologię, zatem można wyjść z założenia, skoro przedsiębiorstwo wykorzystuje ERP do planowania produkcji lub przynajmniej posiada takowy system to powinno mieć w nim opracowaną technologię produkcji. I tak zazwyczaj jest z technologią materiałową – BOM, która dla MRP jest w zupełności wystarczająca. Technologia operacyjna (lista poszczególnych operacji dla wykonania konkretnego wyrobu) nie była wykorzystywana do planowania produkcji, zatem nie było większego sensu by ją założyć w systemie ERP przed laty. Wystarczyło wprowadzenie jednej operacji oraz BOM by planować i rozliczać produkcję. Stosując jednak system APS będzie inaczej. Mamy zatem pracę domową do odrobienia. W tym momencie bywa, że pojawia się problem, bowiem okazuje się że obecne rozwiązanie IT, w którym mamy zbudowaną technologię materiałową np. jakiś system typu ERP z jakichś względów jest ułomne w obszarze technologii. Zazwyczaj jeśli nie mniejszym to większym nakładem czasu i pieniędzy istnieje możliwość wprowadzenia do niego technologii operacyjnych. Niemniej jednak nie zawsze w idealnym modelu tzn. tworzymy oddzielnie technologię BOM i niezależnie technologię operacyjną, która może być wykorzystywana dla wielu wyrobów. Takie podejście pozwala na łatwiejsze zarządzanie zmianami w technologii, brak konieczności dublowania zakładanych technologii i ich powielania dla poszczególnych wyrobów oraz łatwiejszą integrację z systemem APS.
Technologia powinna umożliwiać definiowanie tzw. nakładkowania na siebie operacji produkcyjnych tj. zdefiniowanie po ilu sztukach, dla których wykonano operację produkcyjną X możemy przejść do realizacji kolejnej operacji produkcyjnej celem rozpoczęcia jej wcześniej niż po ukończeniu 100% sztuk. Znów nie każdy system ERP daje możliwość uwzględnienia wielu parametrów w tym zakresie, czasem ograniczając się ewentualnie jedynie do jednostki czasu określającej przesunięcie. Szczególnie w przypadku dużej ilości wyrobów tudzież ich wersji istotną funkcją jest możliwość optymalizacji podmiany surowca/komponentu tudzież operacji w grupie technologii w możliwie jak najprostszy sposób (ograniczając się do możliwie jak najmniejszej ilości kliknięć). Podobnych narzędzi optymalizacyjnych poszukuje się przy tworzeniu nowych technologii. >W produkcji wykorzystującej formy, należy zauważyć, iż te powinny być wiązane z konkretnym półproduktem i konkretną operacją w marszrucie, a nie wyrobem gotowym i całą marszrutą. Tym samym jeśli marszruta obejmuje przykładowo operacje: 10 – spawanie, 20 – kontrola jakości, 30 – obróbka termiczna etc. to nasza forma do spawania powinna zostać powiązana wyłącznie z operacją 10 i tylko ta operacja powinna pochłonąć zasób w postaci tejże formy.
Co jednak zrobić jeśli stosowane rozwiązanie typu ERP nie pozwala tudzież opracowanie tej technologii jest bardzo kłopotliwe?
No cóż trzeba powiedzieć najpierw, że z wielu względów technologia powinna być w systemie ERP. Tam jednak funkcjonuje pętla MRP, tam mamy informacje o zapasach i to tam zazwyczaj prowadzimy kalkulacje. Jednak nie tak dawno u jednego z naszych klientów, a była to średniej wielkości firma produkująca urządzenia zdecydowaliśmy się wspólnie na zupełnie inne podejście. Przedsiębiorstwo było na końcowym etapie aktualizacji stosowanego oprogramowania ERP i w fazie podnoszenia jego wersji podjęło już próby zbudowania pełnej technologii (BOM, marszruty) wraz z wersjami wyrobów w tymże oprogramowaniu. Prace te zakończyły się fiaskiem. Rozpoczęły się poszukiwania systemu MES, który miał uzupełnić ERP w obszarze zarządzania produkcją i tym samym wrócił temat planowania produkcji. Idealnie by było zasilić MESa aktualnym planem produkcji, a nie Arkuszem Excel czy kartką papieru…
No a skoro już pojawił się temat planowania produkcji to szybko wrócił zakopany w niepamięć wątek technologii. W zasadzie stwierdziliśmy, że do opracowania technologii w tym systemie ERP można podejść raz jeszcze, być może z innym zespołem po stronie dostawcy systemu – bardziej kompetentnym, aczkolwiek nieuniknione są dodatkowe koszty wynikające z prac programistycznych jakie dostawca musi ponieś by dostosować system do brakujących funkcjonalności. Jednocześnie to będzie mozolne i opóźni znacząco proces wdrożenia APS i MES. Szybko przeanalizowaliśmy alternatywne warianty i zasadniczo nasunął się w tym przypadku jeden. Sięgnijmy po rozwiązania APS, które posiadają moduł technologiczny tudzież ich dostawca może zaoferować jakiś uzupełniający komponent do oferowanego APS, którym pokryje nasze potrzeby w zakresie technologii. Za tym wariantem przemawiał jeszcze jeden fakt, jakim była przewidywana zmiana systemu ERP na rozwiązanie korporacyjne w przeciągu kilku lat. Po kilku prezentacjach nikt już nawet nie myślał by próbować budować technologię w stosowanym ERP. Managerowie zobaczyli gotowe rozwiązanie dające szereg dodatkowych możliwości i ergonomii pracy przy zakładaniu nowych technologii, pracy nad bieżącymi czy ich wersjonowania co było nieporównywalne do tych narzędzi dostępnych w ERP. Oczywiście coś za coś. Bardziej kłopotliwe stały się kalkulacje, jednakże wspólnie z dostawcą systemu ERP dokonano precyzyjnej integracji tychże aplikacji ze sobą co w rezultacie pozwoliło przedsiębiorstwu stwierdzić, iż podjęto wówczas trafną decyzję. Zatem choć naturalnym środowiskiem dla tworzenia i utrzymywania technologii jest ERP to w razie potrzeby istnieją alternatywy.
Kluczowe jednak jest by miejsce powstawania i utrzymywania technologii było jedno, a nie rozproszone w kilku aplikacjach.
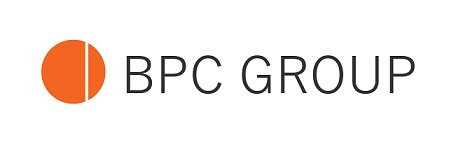