Aby omówić problemy branży metalowej należy najpierw określić z jakiej grupy jest dane przedsiębiorstwo:
- Czy jest to firma zajmująca się dystrybucją metali lub wyrobów z metali, gdzie największe problemy to różnorodność rozmiarów tego samego produktu?
- Czy może jest to przedsiębiorstwo zajmujące się wytopem metali lub wyrobów z metali, gdzie jednym z podstawowych trudności jest wychwycenie kosztu surowca dla danej grupy zleceń (charakterystyczny problem w firmach realizujących produkcję procesową)?
- Czy jednak jest to firma z branży obróbki metali charakteryzującej się jeszcze innymi wyzwaniami?
„Charakterystyczne problemy przedsiębiorstw branży metalowej” – brzmi niewinnie, a jakie niesie ze sobą konsekwencje ! Produkcja na zamówienie, krótkie partie, rozbudowany park maszynowy, zróżnicowana produkcja gniazdowa, częste zmiany i konieczność przezbrojeń, rozliczanie kosztów narzędzi i zleceń … Brzmi znajomo ? No cóż to codzienność branży obróbki metali.
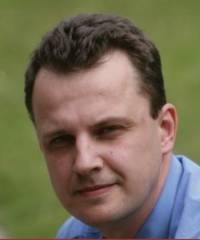
Adam Gębski,
Dyrektor sprzedaży,
L-Systems Polska
Płynnie, na czas, bez niespodzianek czy „ogonów” – czyli jak sprawnie realizować proces produkcji i wychwytywać niezgodności?
Tylko bieżąca informacja na temat stopnia zaawansowania produkcji stanowi podstawę do sprawnej jej realizacji. Pozwala to na wczesną identyfikację problemów. Niestety bardzo często raportowanie produkcji odbywa się w firmach z bardzo dużym opóźnieniem. A przecież można to w łatwy sposób usprawnić.
Częstą sytuacją jest również, konieczność modyfikacja technologii w ramach już otwartego zlecenia. Ukierunkowanie na coraz lepsze zaspokajanie potrzeb klientów oraz rosnące i wymagania powodują, iż często zgadzamy się na poważne zmiany już w trakcie realizacji zlecenia. Charakterystyczne są także częste zmiany w dostępnych surowcach (wycofanie przez producentów danego typu surowca, czy ich dostępność na rynku itp.), które wymuszają u producentów branży obróbki metali zmiany w strukturze materiałowej zdefiniowanej wcześniej na potrzeby produkcji. W jednej technologii nie jest to trudne, ale zamiana indeksu w setkach czy tysiącach technologiach produkcyjnych gdzie został on użyty to już duże wyzwanie.
W odpowiedniej ilości, najtaniej, w odpowiednim momencie – czyli jak zapewnić niezbędne surowce na czas bez zbędnych nad stanów magazynowych ?
Minimalizacja zapasów magazynowych przy jednoczesnym zapewnieniu ciągłości produkcji to niekończące się wyzwanie jakie stoi przed działem zakupów. Codzienne wyzwania to bardzo duża wariantowość rozmiarów tego samego indeksu, różnorodność używanych jednostek miar, zapewnienie identyfikacji konkretnego surowca przypisanego do danego zlecenia produkcyjnego, optymalizacja cen zakupu (grupowanie ilości zakupowych, łączenie dostaw od tego samego dostawcy itp.). Gwarancja terminowości i jakości dostaw wymaga także systematycznej klasyfikacji i oceny dostawców.
Więcej, szybciej i dokładniej – czyli jak sprawnie przeprowadzić proces ofertowania?
Duża liczba przygotowywanych ofert wymaga odpowiedniego przepływu zadań (workflow) obejmującego wiele działów w firmie: sprzedaży, technologii, produkcji, planowania, zaopatrzenia. Na bazie dokumentacji klienta potrzeba jest szybka informacja na kiedy i za ile możemy dany element wykonać. Ze względu na znaczną fluktuację cen surowców w tej branży kalkulacja kosztów powinna uwzględniać także przewidywane ceny surowców w przyszłości.
Rentowność, zarobek, zysk – czyli ile to nas tak naprawdę kosztowało ?
Rozliczanie kosztów produkcji to potrzeba bardzo szczegółowego ich raportowania i śledzenia w trakcie realizacji zleceń. Analiza opłacalności zamówień, zleceń produkcyjnych, detali (produktów), a także obserwacja ich rentowności na różnych poziomach marż to kolejne wyzwania, z którymi na co dzień borykają się firmy. Nie łatwo jest przecież jednoznacznie przypisać koszty do konkretnych zleceń produkcyjnych.
Podnoszenie (jakości), minimalizacja (reklamacji) – czyli jak zapewnić odpowiednią jakość naszych wyrobów?
Kontrola jakości to kolejny ważny element, choć nie zawsze stosowany w rozbudowanym zakresie. Realizowana zarówno przy przyjęciu surowców na magazyn, jak i na różnych etapach zlecenia produkcyjnego. Kontrola jakości staje się dużo bardziej ważna w przypadku konieczności spełnienia wysoko postawionych wymogów jakościowych branż odbiorców. Jak ją ustawić, aby zapewnić wysokiej jakości wyroby jednocześnie nie powodując zbędnych zastojów w procesie produkcyjnych?
EPICOR ERP
Wybrane funkcje systemu dedykowane przedsiębiorstwom branży obróbki metali, w tym firm o profilu produkcyjnym MTO (produkcja na zamówienie):
- Definiowalny, zadaniowy workflow ofertowania;
- Harmonogram co jeśli ? Czyli informacja na kiedy możemy dostarczyć zamówienie, jeżeli oferta byłaby zaakceptowana dzisiaj ?
- Advanced Production Scheduling (zaawansowane harmonogramowanie produkcji – w tym tablica harmonogramowania zasobów) pozwalający na symulację, zmiany oraz analizę obciążeń gniazd roboczych;
- Pulpit zaopatrzeniowca oraz Doradca zakupów – wszystkie informacje (Co ? Na kiedy? Od kogo? Za ile ?) w jednym miejscu;
- SRM (zarządzanie relacjami z dostawcami) – analizy dostawców, zapytania ofertowe i wsparcie dla wyboru ofert;
- Definiowalne jednostki miar i opakowań zbiorczych;
- Data Collection (MES) – bieżące raportowanie postępów na produkcji ;
- Zarządzanie wyjątkami – alerty niezgodności z planem produkcji;
- Monitory lokalizacji Kanban – wsparcie dla produkcji odchudzonej (Lean);
- Job Tracker – w jednym miejscu wszystkie informacje o zleceniu. M.in. o jego realizacji i kosztach w odniesieniu do wartości planowanych;
- Zaawansowane rozliczenie kosztów produkcji i analiza ich rentowności;
- Advanced Quality Control – defniowalne plany kontroli jakości zapewniające wsparcie dla Advanced Product Quality Planning, Production Part Approval Process, Statistical Process Control, Cp,Cpk,Pp,Ppk, oraz wszelkiego typu analizy i raportowanie w tym wykresy i histogramy;
- Traceablity dashboards – defniowalne raporty/analiza z jakich materiałów, od jakiego dostawcy, na jakich gniazdach roboczych został wykonany dany produkt/element.
Zobacz więcej informacji o rozwiązaniu na stronie wyszukiwarki BPC Guide.