Wdrożenie Systemu ERP jest kluczowym etapem w transformacji cyfrowej wielu firm. Jest to kompleksowy proces, który wymaga starannego planowania, odpowiedniej metodyki oraz efektywnego zarządzania projektem. Sukces we wdrożeniu systemu ERP może przynieść wiele korzyści, takich jak usprawnienie procesów biznesowych, zwiększenie efektywności działania firmy oraz poprawa jakości obsługi klienta. Jednakże, aby osiągnąć te korzyści, niezbędne jest właściwe przygotowanie, odpowiednie zasoby oraz skuteczne zarządzanie całością procesu wdrożenia. W niniejszym artykule omówimy metodologię wdrożenia systemu ERP oraz kluczowe aspekty zarządzania projektem, które mogą przyczynić się do osiągnięcia sukcesu w tym obszarze.
- Realistyczne oczekiwania
Jasność i otwartość to fundament, na którym powinien opierać się każdy dostawca systemów zintegrowanych. Niezależnie od specyfiki procesów biznesowych w firmie, uczciwość wobec klienta musi być zachowana przez cały czas współpracy. Zanim ERP zostanie uruchomiony, kluczowe jest przeprowadzenie spotkań z ekspertami od potencjalnego dostawcy. Ich zadaniem jest dogłębne zrozumienie działalności firmy oraz pokazanie, w jaki sposób ich system może wspierać i usprawniać codzienną pracę przedsiębiorstwa.
Priorytetyzacja jest następnym krokiem, który należy uwzględnić przy wdrażaniu systemu ERP. Życie często opisuje się jako szereg wyborów, a w kontekście implementacji systemu zintegrowanego ta zasada znajduje pełne zastosowanie. Realizacja określonych celów wdrożeniowych wiąże się z konkretnym nakładem finansowym. Przydzielając priorytety celom, a najlepiej konkretnym obszarom wraz z zadaniami, można skupić się na osiągnięciu tych najistotniejszych, odkładając mniej ważne na później. Takie podejście nie tylko pozwala na głębsze poznanie standardowych funkcjonalności wybranego systemu, unikając jednocześnie zbyt skomplikowanych dostosowań, ale również otwiera drogę do oszczędności w zakładanym budżecie wdrożeniowym. Zastosowanie zasady Pareto, czyli skoncentrowanie się na tych 20% działań, które przyniosą 80% wartości, może znacząco przyspieszyć uzyskanie korzyści z nowego systemu ERP. Następnie, już z solidną bazą, firma może kontynuować dopracowywanie i optymalizację wdrożonego rozwiązania.
- Przewodnik: Jak unikać pułapek w projektach ERP?
W dzisiejszym dynamicznie rozwijającym się świecie biznesu, znaczenie czerpania wiedzy z doświadczeń, zarówno własnych, jak i obcych, jest nie do przecenienia. Literatura biznesowa obfituje w dzieła dotyczące uczenia się, adaptacji organizacji do zmieniającego się otoczenia oraz idei ciągłego doskonalenia, które są kluczowe w procesie implementacji systemów ERP. Sukces wdrażania takiego systemu zależy od wielu czynników, nie tylko w fazie implementacji, ale już na etapie przygotowań. Wybór odpowiedniego modelu współpracy z dostawcą to dopiero początek. Istnieje kilka kluczowych zasad, wywodzących się ze zwinnych metodologii tworzenia oprogramowania, które, uzupełnione ponad 30-letnim doświadczeniem BPSC w pracy z niemal 300 przedsiębiorstwami, kształtują jakość i efektywność wdrożenia systemu zintegrowanego, jakim jest BPSC ERP.
Priorytet ludzi nad procesami: Zaangażowanie i motywacja zespołu projektowego są fundamentem sukcesu. Bez zrozumienia i akceptacji celów projektu przez użytkowników końcowych, każdy system jest skazany na porażkę. Kluczowe jest więc budowanie relacji i współpracy, które umożliwiają osiągnięcie zamierzonych rezultatów.
Funkcjonalność nad dokumentacją: Dokumentacja jest ważna, ale nie powinna dominować nad działaniem systemu. Dynamiczne środowisko biznesowe wymaga elastyczności i gotowości do adaptacji, co oznacza, że dokumentacja, choć niezbędna, nie może hamować postępu projektu. Praktyczna użyteczność i efektywność rozwiązania są nadrzędne.
Współpraca nad negocjacjami: Budowanie trwałych i opartych na zaufaniu relacji z klientem jest kluczowe. W polskich realiach biznesowych, gdzie sceptycyzm często dominuje, ważne jest wyjście poza schematy i stawianie na otwartą komunikację oraz budowanie partnerstwa długoterminowego, zamiast skupiania się na rygorystycznych warunkach umów.
Elastyczność nad sztywnym planowaniem: Ścisłe trzymanie się pierwotnego planu w obliczu zmieniającej się rzeczywistości biznesowej może być przeszkodą. System klasy ERP, ze względu na swoją złożoność i mnogość dostępnych funkcji, wymaga otwartości na zmiany i dostosowanie do aktualnych potrzeb. Planowanie jest ważne, ale musi iść w parze z gotowością do modyfikacji i adaptacji, co pozwala na optymalizację wykorzystania zasobów i efektywne korzystanie z systemu.
Takie podejście do wdrażania systemów ERP nie tylko zwiększa szanse na sukces, ale także pozwala na budowanie trwałej wartości i konkurencyjności firmy w zmieniającym się świecie biznesu.
- Co tworzy doskonałe wdrożenie ERP? Bo idealnego nie ma!
Wizja perfekcyjnego wprowadzenia ERP-a jest często uważana za cel osiągalny tylko w świecie teorii i idealnych założeń. Taki bezbłędny projekt mógłby się udać wyłącznie w przedsiębiorstwie z nieograniczonymi funduszami, które dodatkowo planuje rozpoczęcie budowy nowej fabryki. Mimo że taki obraz może wydawać się nieosiągalny, nie oznacza to, że każde wdrożenie lub aktualizacja systemu zarządczego jest skazana na niepowodzenie. Analogia do kręgosłupa ma na celu podkreślenie, jak bardzo software jest niezbędny do zarządzania kluczowymi procesami informacyjnymi w firmie. To podkreśla, że proces wdrożenia zbliżony do ideału, choć wymagający, jest możliwy do zrealizowania pod pewnymi warunkami.
- Klient ma wyraźnie określone cele, które chce osiągnąć dzięki wybranemu oprogramowaniu ERP.
- Klient jest świadomy metodologii wdrożenia i wyznacza osoby z pełnymi uprawnieniami do podejmowania decyzji biznesowych dotyczących projektowanego rozwiązania.
- Dostawca od samego początku jest całkowicie otwarty w procesie sprzedaży aż do momentu uruchomienia systemu, co buduje zaufanie klienta.
- Zespoły po obu stronach są w pełni zaangażowane i świadome nakładu czasu wymaganego do pracy.
- Harmonogram prac i zadania są planowane wspólnie przez przedstawicieli dostawcy i klienta w określonych ramach czasowych.
- Po każdym etapie pracy, zespoły wspólnie omawiają, co się udało, a co wymaga zmiany, by proces był jeszcze lepszy, wprowadzając te ulepszenia w następnych iteracjach.
- Projektem kieruje zasada maksymalizacji standardowych możliwości oprogramowania, szukając dopasowania do specyficznych potrzeb tylko, gdy jest to efektywne po uruchomieniu systemu.
- Cele i zadania w poszczególnych etapach wdrożenia są ustalane wspólnie, co ułatwia szacowanie wymaganej pracy.
- Wdrożenie ma wyznaczone ramy czasowe i budżet, ale szczegółowe wykorzystanie środków jest dostosowywane do bieżących potrzeb i priorytetów.
- Zespół wdrożeniowy ze strony dostawcy jest stabilny i zapewnia wsparcie dla określonej grupy klientów przez cały proces, uzupełniając zespół wsparcia produktu dostępnego od momentu podpisania umowy.
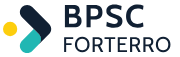