1. Czym powinien się charakteryzować prawidłowo wdrożony w firmie produkcyjnej Total Productive Maintenance?
Ewolucja nie rewolucja,
Kto nie słyszał o magii liczb: 8 filarów TPM, zero strat, 5 why, 5s itp.? Natomiast w naszej opinii prawidłowo wdrożony TPM to nie zmiany rewolucyjne, a ewolucyjne, drobne, sukcesywnie wprowadzane i co najważniejsze praktyczne, używane na co dzień, pomagające w codziennej pracy. To prowadzi do poprawy jakości przy jednoczesnym dbaniu o stabilność w ogólnie pojętym zarządzaniu.
Zmiana podejścia nie tylko w utrzymaniu ruchu
Jeśli TPM będzie obejmował jedynie UR to może się okazać, że dochodzi do rozminięcia się koncepcji z rzeczywistością. Jeśli przedsiębiorstwo stawia jedynie pytanie jak zwiększyć obroty przy obniżeniu kosztów to brakuje najważniejszego pytania które stawia TPM: Jak podnieść jakość, aby nie kosztowało nas to więcej niż to co robimy obecnie? Myślenie kategoriami jakości się opłaca.
Opłaca się, ale… efekty przychodzą później. Jeśli nie ulegamy chęci tylko błyskawicznych efektów to TPM jest dla nas.
To ciągły proces
Dobry TPM to taki, który „się uczy”, zbiera dane analizuje i wyciąga wnioski. Czy wiem, które spośród moich maszyn są najbardziej awaryjne?
Dlaczego podobne pompy wymagają różnych nakładów na utrzymanie? Czy potrafię przypisać koszt-y do maszyn? Czy znam dane historyczne i planowane działania? Czy dobieram strategie UR w zależności od poziomu krytyczności maszyn? Czy przy określaniu krytyczności uwzględniam sposób wykorzystania danego urządzenia oraz jego sezonowość?
Jeśli po wdrożeniu została nam masa martwych zasad i kilka nowych narzędzi to coś poszło nie tak. Co? TPM to nie jednorazowe działanie, tylko ciągły proces w myśl tzw. cyklu Deminga PDCA: Plan Do Check Act . Planuj, działaj, sprawdzaj, poprawiaj i od nowa. Jeśli zaszczepimy tę myśl na każdym poziomie organizacji, nasza załoga będzie zaangażowana w ten proces i co najważniejsze będziemy wierzyć w efekty – to znaczy mamy wdrożony TPM.
2. Jakie działania rekomendujecie Państwo klientom w celu właściwego zarządzania i utrzymania sprawności maszyn? Czy proponujecie jakieś systemowe rozwiązania w tym zakresie?
Jako integrator dla przemysłu z pewnością polecamy zrobić duży krok w stronę TPM wdrażając systemowe rozwiązanie w postaci systemu IT klasy EAM/CMMS, w którym „zaszyte” są jego (TPM-owe) zasady i który nam o nich przypomina. Polecamy rozwiązanie AIUT, które nazwaliśmy Maximo Express, bo łączy system IBM Maximo Asset Management (światowy lider systemów CMMS) z nowym podejściem do wdrożenia, które umożliwia niemal ekspresową implementację na tle standardowego podejścia uwzględniając gotowe funkcje i moduły. Dużym atutem jest też dużo niższa cena . Szczegóły znajdą Państwo na www.mex.maximo.pl .
Jak pamiętać o wszystkich pracach – zapobiegaj zamiast leczyć
System komputerowy umożliwia planowanie i harmonogramowanie pracy, w tym również automatyczne. Może generować zlecenia w oparciu o harmonogramy czasowe, czy odczyty z urządzeń, jeśli te wykraczają poza założone normy.
Skąd te awarie – zbieraj wiedzę i wyciągaj wnioski
CMMS/EAM umożliwia gromadzenie danych o wszystkich wykonywanych pracach, zarówno planowanych jak i awaryjnych oraz alokować koszty zarówno na urządzeniach, jak i miejscach ich wykorzystania, co jest szczególnie ważne przy urządzeniach rotacyjnych. Spójne, kompletne i wiarygodne dane to podstawa wszelkich analiz np. dlaczego rzeczywistość odbiega od planów, jakie są najczęstsze przyczyny awarii itp.
Mamy awarię – reaguj błyskawicznie
Dobry system wspierający TPM posiada również proste aplikacje dla pracowników spoza UR, w szczególności do rejestrowania zgłoszeń i komunikacji z działem technicznym. Przyjazne aplikacje, w tym na urządzenia mobilne, pozwolą nie tylko szybko dokonać zgłoszenia awarii, ale także zapewnią dostęp do niezbędnej dokumentacji, czy na bieżąco wprowadzać dane z przeglądów i odczytów.
Wskaźniki – OEE, MTTF, MTBF, MTBR
Jak to liczyć? System zrobi to za ciebie, co więcej – powiadomi o zbliżeniu się do niepożądanego poziomu wskaźnika, dając czas na podjęcie działań w sposób proaktywny.
3. Jak oceniacie Państwo świadomość menadżerów utrzymania ruchu w zakresie TPM i utrzymania maszyn w gotowości do pracy?
Świadomość w UR w tym względzie jest wysoka, co widać po pytaniach zadawanych podczas różnego rodzaju targów i spotkań zarówno z obecnymi, jak i (mamy nadzieję) przyszłymi klientami. W mojej naszej opinii należy zadać pytanie – co ze świadomością biznesu? Jak „sprzedać” to, że warto wdrażać TPM i jego narzędzia? Tu często pojawiają się przysłowiowe „schody”. Przecież TPM to nie tylko zasady, to też (a może przede wszystkim) korzyści, i to nie tylko finansowe, jednak na początkowym etapie wymagające często zwiększenia nakładów na UR.
Na przykład :
– skoro dbam o park maszynowy poprzez prawidłową prewencję i predykcję, to będzie mniej awarii i skrócę przestoje,
– jeśli odpowiednio planuję prace, to mogę zamówić materiał tuż przed, a nie przechowywać go na magazynie i w ten sposób obniżam stany magazynowe.
Korzyści oczywiście można wymienić znaczenie więcej, jeśli interesuje Państwa co może jeszcze osiągnąć poprzez wdrożenie systemu CMMS/EAM zapraszamy do kontaktu.
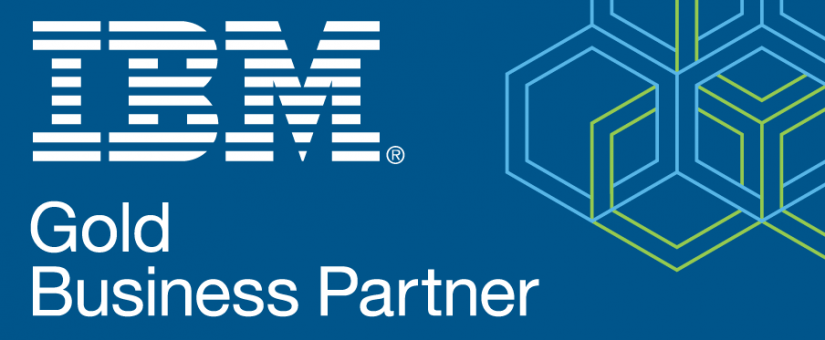
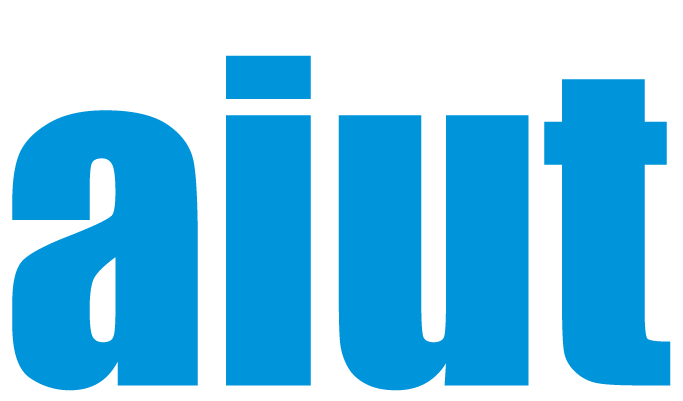
AIUTJest partnerem firmy IBM od 1998 r. i obecnie posiada jeden z najwyższych poziomów autoryzacji status Gold Business Partner potwierdzający wysokie kompetencje i doświadczenie.
AIUT to globalny dostawca zrobotyzowanych linii i stanowisk produkcyjnych, systemów automatyki, elektryki przemysłowej i IT oraz rozwiązań IoT.
Mateusz Iwanicki – AIUT Specjalista ds. sprzedaży, dział systemów IT EAM. Pomaga pracownikom Służb Utrzymania Ruchu w zakresie usprawnienia pracy, planowania, optymalizacji kosztów, skracania postojów i zmniejszeniu liczby awarii dzięki systemom firmy IBM. Prywatnie ojciec, siatkarz i miłośnik rodzimych Bieszczad.
Maciej Guzek – AIUT Certyfikowany konsultant i trener Maximo z kilkunastoletnim doświadczeniem w realizacji wdrożeń systemów zarządzania majątkiem i usługami zarówno w Polsce jak i za granicą. Analityk biznesowy i certyfikowany Project Manager. Prywatnie – zapalony żeglarz, oddany mąż i ojciec 4 dzieci.