Modernizacja Przestarzałych Parków Maszynowych w Kierunku Inteligentnych Fabryk
Cyfrowa transformacja i integracja produkcji w sieć stanowią kluczowy cel nowej ery Przemysłu 4.0. W teorii, zakłady produkcyjne idealnie projektowane i budowane od zera przyjmują podejście Greenfield. W takich przypadkach maszyny i systemy są wyposażone w czujniki monitorujące, a narzędzia pracy stają się „inteligentnymi obiektami”, zdolnymi dostarczać informacje o ich aktualnym stanie przetwarzania. Zarządzanie danymi umożliwia głęboką analizę Big Data, na podstawie której można doskonalić i dostosowywać procesy. Jednakże, w rzeczywistości, najczęściej mamy do czynienia z podejściem typu Brownfield. W takich przypadkach przestarzałe parki maszynowe muszą zostać „przekształcone” w inteligentne fabryki. Modułowe rozwiązanie PROXIA MES z wykorzystaniem OPC-UA i XI-Gateway sprawia, że ten proces staje się praktyczny i niezwykle efektywny.
Podejście Greenfield: Życzenie jest ojcem myśli
Temat „cyfryzacji zakładów produkcyjnych” inspiruje obecnie świat zawodowy niemal wizjonerskimi koncepcjami. Mówi się o zaawansowanych technologicznie zasobach produkcyjnych, które współdziałają z systemami opartymi na chmurze i innymi zasobami produkcyjnymi. Mówi się o „systemach cyberfizycznych”, które podejmują decyzje samodzielnie, na podstawie zgromadzonych danych. Idee tego „podejścia od podstaw” są genialne. Istnieją prototypy takich „doskonałych” fabryk, gdzie instytucje badawcze wraz z przemysłem testują te koncepcje w praktyce. Jednak te zakłady produkcyjne zostały w większości zbudowane na terenach „zielonych” i nie musiały w żadnym momencie brać pod uwagę żadnych kwestii „dziedzictwa”, takich jak istniejące maszyny.
Podejście do Brownfield: Digitalizacja istniejących struktur
Rzeczywistość, zwłaszcza w średnich firmach produkcyjnych, jest jednak inna. Tutaj napotyka się na historycznie istniejące parki maszynowe. Przy zakupie sprzętu koncentrowano się (i nadal się koncentruje) na technologii. Systemy zostały zakupione w taki sposób, aby wytworzyć jak największą wartość. Myśl o interfejsach i sieci procesowej jest często jeszcze odległa. Teraz jednak firmy odkrywają inny interesujący „efekt” swojej produkcji: dane. Widzą oni, jak ukierunkowane wykorzystanie tych danych może zoptymalizować procesy, zwiększyć wydajność i obniżyć koszty. Nagle dane są coś warte i nabierają ostrości. Jak więc firmy, które nie mają na produkcji „cyfrowych gaduł”, mogą grać w „profesjonalnej lidze” przetwórców danych?
OPC-UA jako podstawa komunikacji w hali produkcyjnej
Zgodnie z mottem „bierzesz, co możesz dostać”, firmy produkcyjne powinny dążyć do rejestrowania wszystkich danych z maszyn. Ważną rzeczą jest tu rozplątanie „sieci protokołów” różnych typów sterowania i instalacji. Celem jest przekazanie danych jak najbliżej miejsca pochodzenia w ramach jednolitej strategii komunikacyjnej. Taka strategia komunikacji powinna nie tylko opisywać dane semantycznie i umożliwiać dwukierunkową komunikację, ale także dbać o aspekty bezpieczeństwa informatycznego. Doświadczenie pokazuje, że luki w zabezpieczeniach są często duże w komunikacji w hali produkcyjnej. Jako rozwiązanie PROXIA OPC-UA pozycjonuje się jako podstawa do komunikacji w hali produkcyjnej, ponieważ wszystkie wyżej wymienione wymagania są spełnione. Kiedy komunikacja jest już „znormalizowana”, wiele różnych systemów może korzystać z tych danych. Ujednolicona komunikacja jest tym, co w pierwszej kolejności umożliwia prawdziwą interoperacyjność różnych uczestników procesu.
PROXIA XI inteligentne i uniwersalne sieci bramowe
W celu zapewnienia tej interoperacyjności PROXIA uruchomiła bramę komunikacyjną. PROXIA XI-Gateway postawiła sobie za zadanie przeniesienie różnych protokołów i interfejsów „świata hali produkcyjnej” do strategii komunikacyjnej OPC-UA. Przykładowo, ogólnie obowiązujące protokoły takie jak „MT-Connect” lub komunikacja specyficzna dla sterowania jak „Heidenhain DNC” mogą być udostępniane bezpośrednio przez OPC-UA. Obecne systemy MES i ERP są w stanie przetwarzać te dane bezpośrednio. W ten sposób wszystkie dane, od prostych informacji o statusie, które są dostarczane przez cyfrowe moduły I/O, do złożonych danych procesowych, które są pobierane ze sterowników instalacji, mogą być dostępne w całym przedsiębiorstwie. Oznacza to, że każde przedsiębiorstwo może wyposażyć swój park maszynowy w „modernizację komunikacyjną” i odpowiednio przygotować się na przyszłe wymagania związane z cyfryzacją produkcji.
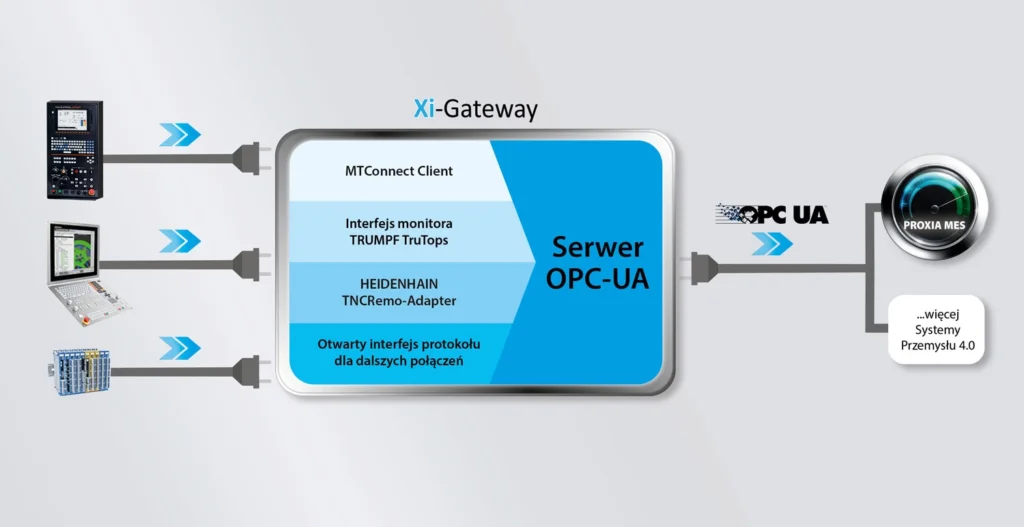