Składowanie blokowe, strategie FIFO/LIFO czy automatyzacja to tylko niektóre sposoby na optymalizację wykorzystywanej przestrzeni. Każda firma ma unikalne potrzeby, więc strategie optymalizacji mogą się różnić w zależności od rodzaju produktów i specyfiki działalności.
W którymkolwiek kierunku nie pójdziemy, kluczowa I tak jest analiza przepływu towarów, która pozwala zrozumieć, jak często, jakie produkty i gdzie się poruszają, co z kolei pozwala na lepsze rozmieszczenie ich w magazynie.
Systemy klasy WMS pozwalają nie tylko zautomatyzować proces analizy, ale i wyciągania z niej wniosków, a w dalszej kolejności podejmowania trafnych decyzji o rozlokowaniu nowych dostaw bądź zmianie lokalizacji dla towarów już zmagazynowanych.
Dzięki pojawieniu się AI, taki proces nie ogranicza się już tylko do dynamicznego slottingu, gdzie bazujemy głownie na klasach rotacji, ale np. posługujemy się dodatkowo regułami asocjacji, pilnując by artykuły, które często występują w zamówieniach razem, były składowane w sąsiednich lokalizacjach.
Poza optymalizacją samej przestrzeni, wpływa to korzystnie na skrócenie długości ścieżek kompletacyjnych, a co za tym idzie optymalizację zasobów.
Wykorzystując digital twin możesz eksperymentować z różnymi typami regałów i ich układami oraz konfiguracjami przechowywania i rozmieszczeniem zapasów bez potrzeby fizycznej zmiany układu.
Symulacja różnych poziomów zapasów i ich rozmieszczenie, pozwala na identyfikację najbardziej efektywnych lokalizacji magazynowania dla różnych typów zapasów. Pomaga to w określeniu najbardziej efektywnej przestrzennie konfiguracji. Wykorzystując dane historyczne i algorytmy predykcyjne, cyfrowy bliźniak może symulować wpływ zmian w układzie lub konfiguracji regałów na wykorzystanie przestrzeni.
Wirtualna wizualizacja przepływu materiałów i procesów magazynowania pozwala zidentyfikować możliwości usprawnienia przepływów pracy i ograniczenia niepotrzebnych ruchów, co również prowadzi do jej efektywnego wykorzystania.
Integracja w czasie rzeczywistym danych z czujników lub z systemu zarządzania magazynem w ramach digital twin umożliwia ciągłe monitorowanie wykorzystania przestrzeni. Pomaga zidentyfikować niewykorzystane obszary lub wąskie gardła, które utrudniają optymalną alokację.
Dane są zbierane w sposób ciągły, dzięki czemu system może sugerować adaptacyjne strategie optymalizacji przestrzeni w oparciu o zmieniające się profile zapasów, wahania sezonowe lub inne czynniki dynamiczne.
Podsumowując, zanim podejmiemy decyzję o inwestycji w nową przestrzeń, dodatkowe zasoby czy automatykę, postarajmy się o porządną analizę przepływów, opartą o rzeczywiste dane z naszych operacji. Pamiętajmy tu o starej zasadzie, że jaka jakość danych wejściowych, taki wynik analizy. Zanim zaczniemy analizę, upewnijmy się więc, że dane, którymi dysponujemy są aktualne, wiarygodne i miarodajne – tylko wtedy nasze późniejsze decyzje przyniosą pożądane efekty.
Grzegorz Prorok, Dyrektor zarządzający w Consafe Logistics
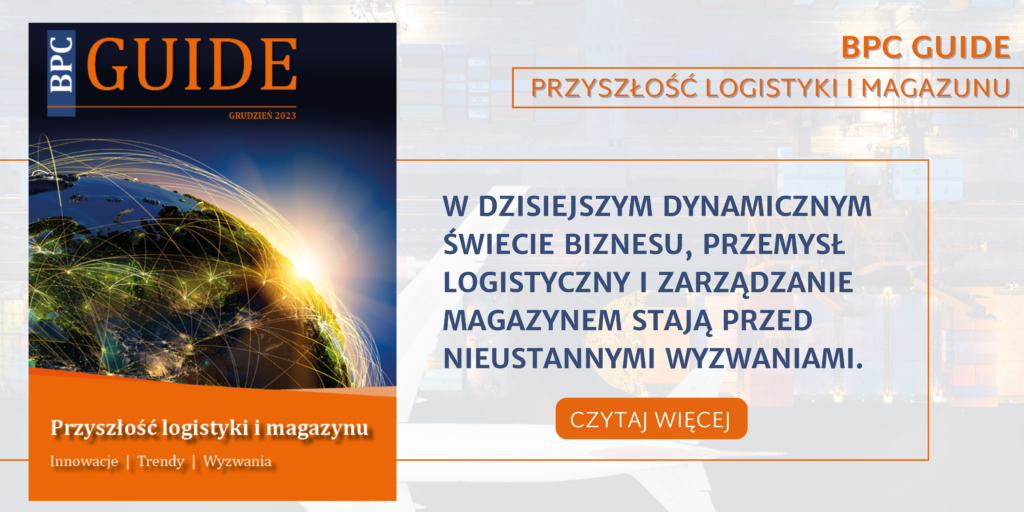