Wczesne wykrycie nieprawidłowości w pracy maszyn to klucz do uniknięcia kosztownych przestojów produkcyjnych. Jednym z najskuteczniejszych sposobów kontroli stanu technicznego urządzeń są obchody zmianowe – regularne trasy inspekcyjne realizowane przez pracowników produkcji lub działu utrzymania ruchu.
Dlaczego warto wdrożyć obchody zmianowe?
W wielu zakładach awarie, które doprowadziły do zatrzymania produkcji, mogły zostać wykryte wcześniej – wystarczyła cykliczna kontrola i reakcja na wczesne symptomy. Problemem bywa brak systemowego podejścia: obchody są prowadzone nieformalnie lub dokumentowane wyłącznie na papierze, co utrudnia analizę i nadzór.
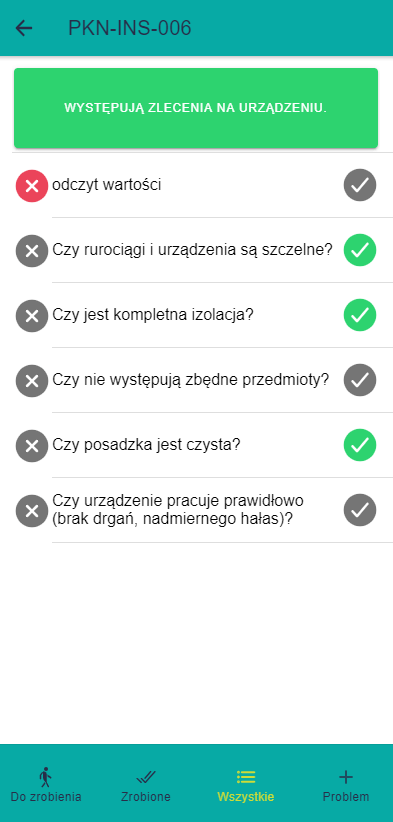
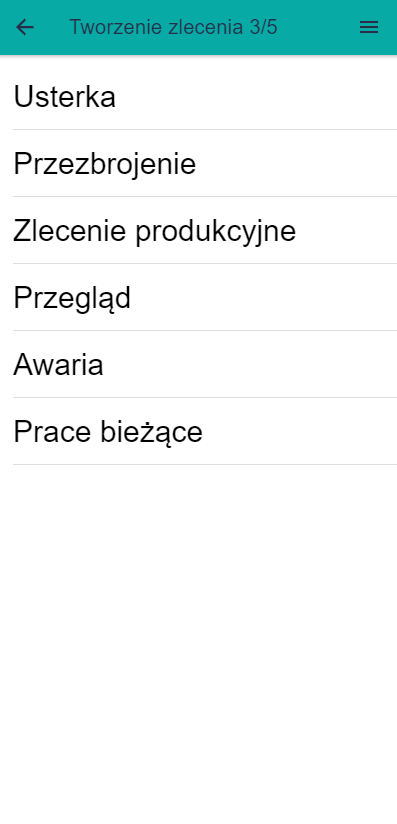
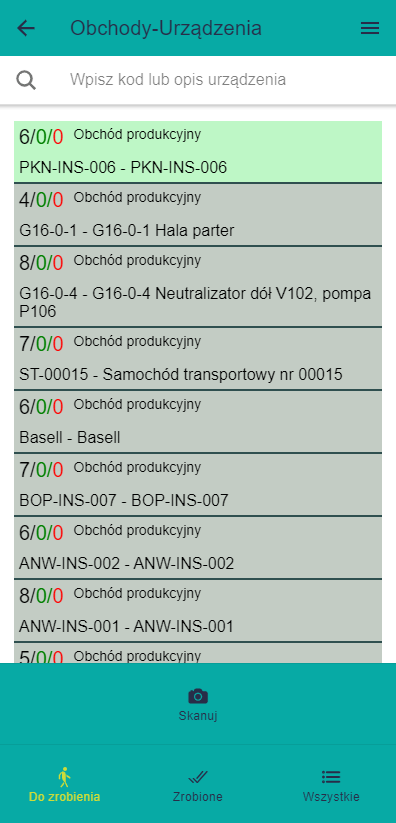
Nowoczesne narzędzia wspierające obchody
Standardową procedurą mającą na celu prowadzenie tego typu działań jest „obchód zmianowy” realizowany najczęściej przez pracowników produkcji w ramach coraz bardziej popularnej strategii Autonomicznego Utrzymania Ruchu (Autonomous Maintenance).
Zdarza się również, że tego typu działania prowadzone są również przez pracowników służb technicznych, co wynika najczęściej ze struktury organizacyjnej i podziału odpowiedzialności. Niezależnie od tego jaki dział jest odpowiedzialny za realizację obchodów, często zakres tych działań nie jest ujęty w żadnym systemie informatycznym i pozostaje jedynie w wersji papierowej.
Co obejmuje nowoczesny system obchodów?
- Ewidencja ścieżek obchodowych wraz z częstotliwością wykonania
- Definicja zakresu kontroli dla poszczególnych urządzeń wchodzących w zakres ścieżki obchodowej
- Określenie zakresu oczekiwanej odpowiedzi od realizującego obchód np. wprowadzenie wartość kontrolowanego parametru, potwierdzenie wykonania „czynności”, itp.
- Urządzenie mobilne typu Tablet lub Smartfon do potwierdzania wykonanych czynności podczas realizacji obchodu
- Oznakowanie trasy obchodowej z wykorzystaniem technologii RFID / NFC, która wymusi obecność pracownika na instalacji i usprawni rejestrację „danych”
- Mechanizm do szybkiej rejestracji zidentyfikowanych problemów obejmujący klasyfikacją i dokumentacją zdjęciową
- Intuicyjne i proste w obsłudze narzędzie do analizy i nadzoru zrealizowanych obchodów
- Powiadomienia o zidentyfikowanych nieprawidłowościach
Integracja z systemami CMMS / EAM
Tego typu rozwiązanie może działać samodzielnie lub stanowić rozszerzenie istniejącego systemu utrzymania ruchu klasy CMMS / EAM.. To nie tylko poprawa bezpieczeństwa i efektywności, ale także realne wsparcie dla strategii Autonomicznego Utrzymania Ruchu (Autonomous Maintenance).