- Według badania proALPHA: 39 procent małych i średnich przedsiębiorstw potwierdza, że przepisy dotyczące łańcucha dostaw i ochrony klimatu mają silny wpływ na ich działalność.
- W porównaniu branż: 43 procent przedsiębiorstw produkcyjnych skarży się na negatywny wpływ ustawy dotyczącej łańcucha dostaw na plany ekspansji i międzynarodową konkurencyjność.
Weilerbach, 05 czerwca 2024 r. – Ochrona danych i klimatu oraz ustawa dotycząca łańcucha dostaw mają największy wpływ na niemieckie przedsiębiorstwa małej i średniej wielkości w stosunku do innych przepisów. Potwierdza to aktualne badanie „Niemieckie przedsiębiorstwa średniej wielkości pod presją regulacji” przeprowadzone na zlecenie proALPHA – jednego z wiodących dostawców oprogramowania ERP+ dla sektora małych i średnich przedsiębiorstw. Dla 39 procent małych i średnich przedsiębiorstw niemiecka ustawa o ochronie klimatu i łańcuchu dostaw stanowi hamulec wzrostu lub ekspansji, a ze względu na ogólne rozporządzenie o ochronie danych osobowych (RODO) co trzecia firma (33%) musi zasilić swoją kadrę, aby zapewnić dostawę wymaganych raportów do większych przedsiębiorstw. Porównując branże można stwierdzić, że podczas gdy przemysł wytwórczy oraz sektor handlu, transportu i logistyki borykają się w szczególności z konsekwencjami ustawy o łańcuchu dostaw hamującej wzrost, innowacyjność i inwestycje, branża IT i technologiczna, zwłaszcza w zakresie przepisów dotyczących ochrony danych i klimatu, odnotowuje wzmożone nakłady pracy na raportowanie.
Dla przemysłu produkcyjnego niemiecka ustawa o łańcuchu dostaw stanowi większą przeszkodę dla wzrostu i rozwoju niż wszystkie inne branże analizowane w ramach badania (43% przy średnio 39%). Dodatkowo dla 43 procent badanych przedsiębiorstw w sektorze produkcyjnym, ustawa ta stawia je na niekorzystnej pozycji w kontekście międzynarodowej konkurencji (średnio uważa tak tylko 34% badanych z ogółu branż).
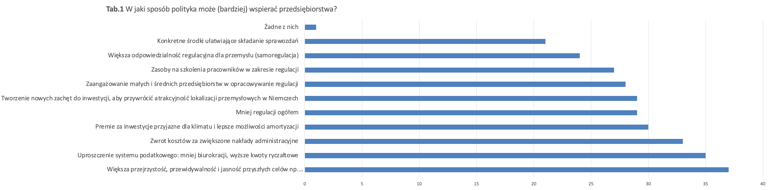
Ponadto Europejski AI Act – pierwsze uregulowanie prawne dotyczące sztucznej inteligencji na świecie – działa jako hamulec innowacji dla przemysłu produkcyjnego (38% w porównaniu do średniej ogółu branż wynoszącej 32%). Również więcej przedsiębiorstw z branży produkcyjnej (34% w porównaniu do 26% średniej ogółu branż) ze względu na europejską ustawę o sztucznej inteligencji chce przenieść swoją produkcję za granicę. Kolejne 32 procent (w porównaniu ze średnią ogółu branż wynoszącą 28%) zgadza się z twierdzeniem, że na skutek tej ustawy Niemcy stracą pozycję lidera międzynarodowej konkurencji.
„Dla przemysłu wytwórczego jest oczywiste, że ustawa dotycząca łańcucha dostaw ma negatywny wpływ w szczególności na wzrost i (międzynarodową) ekspansję. Ponadto według naszego badania europejski AI Act hamuje innowacyjność i osłabia gospodarkę Niemiec”, wyjaśnia Michael Finkler, dyrektor zarządzający ds. Business Development w proALPHA.
Handel, transport i logistyka: regulacje hamują ekspansję i innowacyjność
Dla prawie połowy (44%) przedsiębiorstw handlowych, transportowych i logistycznych (T&L) niemiecka ustawa o łańcuchu dostaw stanowi przeszkodę dla innowacji (średnia ogółu branż wynosi 32%). Również 44 procent w tym sektorze stwierdziło, że europejska ustawa dotycząca łańcucha dostaw zmusza ich do wstrzymania planowanych inwestycji. Średnia dla ogółu branż również tutaj wynosi tylko 32 procent
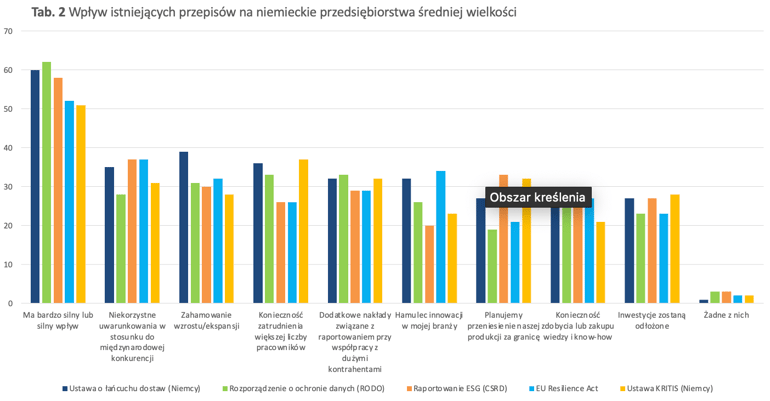
Ponadto handel, transport i logistyka w porównaniu z innymi branżami w większym stopniu odnotowują zahamowanie rozwoju lub ekspansji wskutek europejskiego rozporządzenia o ochronie danych (RODO) (45% w porównaniu do 31%). Konsekwencją jest coraz częstsze odkładanie zaplanowanych inwestycji na później (29% w porównaniu do 23%). Konieczność raportowania w ramach ESG stanowi również silniejszy hamulec inwestycyjny w tym sektorze w porównaniu z innymi sektorami (35% w porównaniu do 26%).
„Wydaje się, że prawodawstwo dotyczące łańcucha dostaw hamuje innowacje i inwestycje w sektorze handlu, transportu i logistyki. Ponadto, w porównaniu z innymi sektorami, raportowanie w ramach ESG oraz rozporządzenie o ochronie danych prowadzą do zmniejszenia możliwości inwestycyjnych i ekspansji” – kontynuuje Finkler.
Branża technologiczna i branża IT: wysokie nakłady na raportowanie
Największym wyzwaniem branży IT i branży technologicznej w zakresie regulacji prawnych jest raportowanie w ramach rozporządzenia o ochronie danych. Prawie połowa głosów (46% w porównaniu do 33% średniej ogółu branż) potwierdza, że RODO oznacza dla nich zwiększony wysiłek przy raportowaniu. Ponadto w obrębie branży technologicznej można stwierdzić, że również małe i średnie przedsiębiorstwa są objęte przepisami prawnymi, które teoretycznie dotyczą tylko dużych przedsiębiorstw. Z tego względu 38 procent (przy średniej wynoszącej 29%) przedsiębiorstw z branży IT i technologicznej stwierdziło, że zasady ESG lub CSRD nakładają na nie wymóg przygotowania dodatkowych sprawozdań, ponieważ więksi kontrahenci (obowiązek ESG dotyczy firm posiadających co najmniej 500 pracowników) wymagają od nich takich sprawozdań.
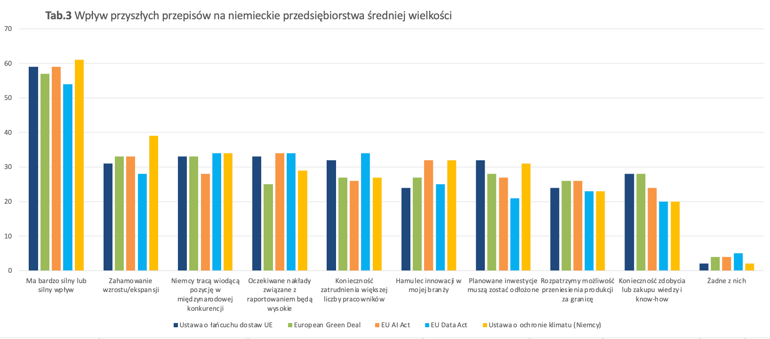
Unijny Resilience Act i ustawa ramowa KRITIS (oba dotyczą w najszerszym znaczeniu bezpieczeństwa informacji) mają negatywny wpływ na innowacyjność, szczególnie w branży IT i technologicznej (potwierdza to 50% ankietowanych, czyli o 16% więcej niż wynosi średnia dla małych i średnich przedsiębiorstw) oraz planowane inwestycje (37% w porównaniu do 27% ogółem). Nie dziwi zatem, że ustawa ramowa KRITIS zmusza szczególnie tą branżę do samodzielnego zdobywania lub nabywania wiedzy z zewnątrz (potwierdza to 41% ankietowanych, czyli o 21% więcej niż średnia ogółem).
„Branża IT i technologiczna częściej niż inne branże skarży się na zwiększony wysiłek przy raportowaniu, również z tego powodu, że nie zmusza ich do tego wielkość własnej firmy, ale wielkość firm kontrahentów objętych regulacjami prawnymi. Ponadto wydaje się, że obecne europejskie przepisy dotyczące bezpieczeństwa, takie jak ustawa ramowa KRITIS i unijny Resilience Act, szkodzą innowacjom i inwestycjom w tym sektorze.”Dyrektor zarządzający ds. Business Development w proALPHA