Wydajność to termin kluczowy w dzisiejszym przemyśle, odpowiednie zorganizowanie pracy zakładu pozwala firmom wywiązać się ze zleceń w terminie, wykorzystując w pełni możliwości swojej załogi. Pomagają w tym specjalistyczne rozwiązania informatyczne.
Jedną z potrzeb firm w XXI wieku jest zwiększanie informatyzacji, czyli poprawa przepływu informacji między realizowanymi procesami. Informacja powinna być szybko zbierana i przetwarzana, by nie traciła na swojej wartości oraz, aby można było na jej podstawie podejmować trafne decyzje – mówi Marek Pomazański – Dyrektor Produkcji w Donako.
Odwiedzamy fabrykę firmy Donako, która specjalizuje się w produkcji komponentów dla elektrowni wiatrowych i wodnych na całym świecie.
Ponad dziewięćdziesiąt procent produktów jest sprzedawanych na rynkach międzynarodowych.
Niewiele osób jest świadomych, że dzięki firmie Donako możemy cieszyć się dłuższą dobą. Firma Donako dostarczała komponenty do budowy największej na świecie hydroelektrowni – tamy trzech przełomów zbudowanej na rzece Jangcy w Chinach. Poprzez przemieszczenie 40 mld ton wody nastąpiło przesunięcie bieguna geograficznego o 2 cm i dzięki temu wydłużenie doby o 6 setnych mikrosekundy – mówi Paweł Dawid – Business Development Manager DSR S.A.
W zakładzie Donako powstają wielkogabarytowe konstrukcje spawane do maszyn elektrycznych wykorzystywanych do produkcji prądu z odnawialnych źródeł energii. Produkowane są tutaj także komponenty np.: blachy pakietu stojana czy wirnika do rdzeni maszyn elektrycznych, wytwarzane są też narzędzia i przyrządy specjalistyczne. Produkcja wykonywana jest na zamówienie, każdy projekt może być zatem inny, a jego realizacja może być rozłożona w czasie.
Na dodatek w jednym momencie w zakładzie wykonywanych jest wiele zleceń. Niezbędne jest zatem monitorowanie przebiegu pracy w czasie rzeczywistym, które pozwala na właściwą ocenę tego, jak naprawdę wykorzystywane są maszyny oraz czas pracy specjalistów.
Jest to możliwe dzięki odpowiedniemu oprogramowaniu – zobaczmy jak ono działa. W zakładzie Donako zastosowany został system SFC 4FACTORY stworzony przez firmę DSR. Do systemu pobierane są dane z systemu ERP. Są to zaplanowane zlecenia robocze do wykonania.
Pracownik przychodząc do pracy loguje się do systemu, w którym otrzymuje kompletną listę czynności, którą w danym dniu ma wykonać na swoim stanowisku pracy. Wybiera zatem zlecenie, którym zamierza się zajmować.
Po uruchomieniu: startu pracy, pracownik wykonuje, to, co mu zostało zlecone. System w tle zbiera informacje na temat czasu pracy przy realizacji danego zlecenia. Po wykonaniu pracy pracownik zmienia status i loguje się do kolejnej operacji lub aktywności, która w danym zleceniu będzie wykonywał. Wszystkie dane trafiają do raportów i są wykorzystywane przy budowaniu wskaźnika efektywności produkcji (OEE) oraz do analizy efektywności pracy pracownika.
Na ich podstawie wyznaczane są czasy realizacji pracy dla poszczególnych zleceń roboczych. Występuje również proces walidacji danych na poziomie mistrza sprawdzającego czy nie doszło do pomyłki, np. błędu manualnego przy ich wprowadzaniu do systemu.
Wybrane raporty SFC 4FACTORY są analizowane przez pracowników działów planowania i kierowników produkcji. Na ich podstawie podejmowane są odpowiednie decyzje. Dzięki wprowadzeniu narzędzia SFC 4FACTORY jesteśmy w stanie monitorować dodatkowe operacje wykonywane przez naszych pracowników, nie ujętych w opisie procesu technologicznego, który jest mocno skomplikowany ze względu na jednostkowy charakter produkcji. Kierownicy produkcji mogą na tej podstawie lepiej zarządzać czasem pracy pracowników oraz wydajniej planować zasoby na kolejne miesiące – mówi Jacek Przechoćko Lider Wdrożenia Systemu w Donako.
Wprowadzenie takich rozwiązań pomogło monitorować przebieg procesów produkcyjnych w zakładzie Donako. Dzięki wdrożeniu systemu SFC 4FACTORY w firmie Donako znacznemu uproszczeniu uległo rozliczanie zleceń produkcyjnych. Pierwotnie informacje wprowadzane były na kartach pracy ręcznie przez pracowników, natomiast obecnie są wprowadzane w formie elektronicznej w systemie SFC 4FACTORY eksportowane do nadrzędnego systemu klasy ERP – QAD Enterprise Applications – mówi Paweł Dawid – Business Development Manager DSR S.A.
Zastąpienie rejestracji pracy na papierowych kartkach systemami informatycznymi staje się koniecznością. Firmy skutecznie konkurujące na międzynarodowych rynkach decydują się na cyfryzację swoich procesów wewnętrznych i sprawiają, że koncepcja Przemysłu 4.0 staje się rzeczywistością również w Polsce.
Tekst i zdjęcia powstały we współpracy z firmą Donako i portalem Fabryki w Polsce.
Przeczytaj więcej o SFC 4FACTORY
Dowiedz się więcej DSR 4FACTORY
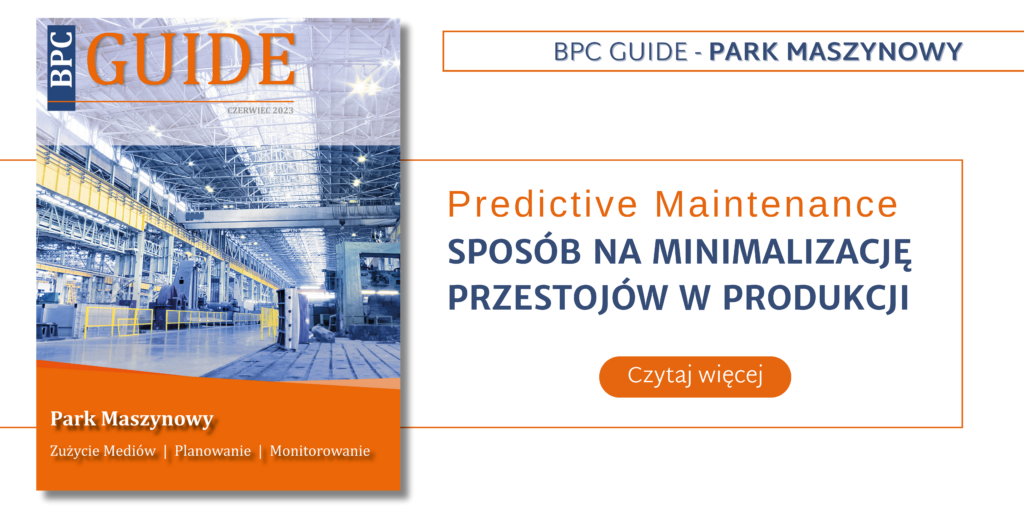