Czym jest produkcja oparta na danych? Jakie korzyści jesteś w stanie dzięki niej osiągnąć? Z jakimi wyzwaniami możesz się mierzyć? Zapraszamy do świata data-driven manufacturing.
Wyniki raportu “Insights-Driven Businesses Set The Pace For Global Growth”, przygotowanego przez ekspertów Forrestera pokazują, że firmy, zorientowane na klienta, które systematycznie wykorzystują dane w całej swojej organizacji i wdrażają je po to, by budować przewagę konkurencyjną za pomocą oprogramowania, rosną średnio o ponad 30 procent rocznie.
Jednocześnie według McKinsey Global Institute firmy oparte na danych mają o 23 razy większą szansę na pozyskiwanie nowych klientów, sześciokrotnie większą na ich późniejsze zachowanie oraz 19 razy większe prawdopodobieństwo, że w rezultacie osiągną zyski. Jest więc o co walczyć!
Data-driven manufacturing w przemyśle
Data-driven manufacturing to podejście do produkcji, które zakłada podejmowanie decyzji na podstawie faktów, a nie domysłów czy przeczucia. Wykorzystuje ono dane, pochodzące z monitorowanych maszyn, od operatorów, pozyskiwane w łańcuchu dostaw oraz z innych źródeł analitycznych, na podstawie których wdrażane są rozwiązania przekładające się na obniżenie kosztów czy zwiększenie wydajności operacyjnej.
Dzięki nowym technologiom coraz większa liczba producentów ma możliwość gromadzenia i przetwarzania danych dotyczących ich działalności, co prowadzi do gwałtownego wzrostu wykorzystania analiz produkcyjnych. Jednak nie wszystkie analizy są takie same. Aby skutecznie wykorzystać dane operacyjne, najpierw należy zebrać dokładne informacje, które później będzie można skutecznie przetworzyć i przedstawić w sposób łatwy do wykorzystania przez użytkownika.
W tym wypadku kluczowe znaczenie ma sposób gromadzenia danych. Ich ręczne zbieranie wymaga nie tylko sporej ilości czasu, ale wiąże się też z dużym prawdopodobieństwem popełnienia błędu. Z drugiej strony gromadzenie danych bezpośrednio z maszyn za pośrednictwem PLC daje bardzo dokładny i obiektywny zbiór danych. Oba rozwiązania w tym wypadku można uznać za „oparte na danych”, ale to drugie jest znacznie skuteczniejsze, a dzięki szybkości ich pozyskiwania i ich większej dokładności umożliwia podejmowanie lepszych decyzji.
Największe korzyści
Rozwój produkcji w oparciu o dane przynosi przedsiębiorstwom przemysłowym szereg korzyści, tj.:
- większa widoczność: na podstawie danych gromadzonych w całej organizacji zarówno specjaliści w hali produkcyjnej, jak i w biurze mogą lepiej określić wydajność przedsiębiorstwa. Dane zapewniają im wgląd nie tylko w indywidualne wyniki, ale także w operacje jako całość. Takie możliwości pomagają osobom decyzyjnym w określeniu słabych punktów, tj.: gorzej pracujące zmiany, powtarzające się przestoje maszyn lub inne wąskie gardła produkcyjne.
- sztuczna inteligencja i uczenie maszynowe: dzięki dużym zbiorom danych producenci mają możliwość uruchamiania algorytmów uczenia maszynowego, które pomagają rozwiązywać złożone problemy oraz stosować zaawansowane praktyki, takie jak konserwacja predykcyjna. Bez dostępu do danych i możliwości ich przetwarzania nie byłyby możliwe nawet uproszczone formy podejmowania decyzji na podstawie danych.
- automatyzacja: istnieją dwie kategorie automatyzacji, które mogą być wykorzystywane w strategiach opartych na danych. Pierwsza z nich to automatyczne zbieranie danych. Jeśli przedsiębiorstwo jest wyposażona w odpowiednie urządzenia do zbierania danych i oprogramowanie do ich przetwarzania, proces nie wymaga już ręcznej pracy. Drugim elementem jest wykorzystanie danych do automatycznego podejmowania decyzji. W miarę rozwoju producenci na swojej analitycznej drodze przechodzą od analizy opisowej do predykcyjnej. Oznacza to, że najpierw wykorzystują dane, aby zrozumieć, co się wydarzyło lub aktualnie się dzieje, ale ostatecznie dojrzewają to tego, by zrozumieć, co może się wydarzyć i dzięki temu mają możliwość reagowania z odpowiednim wyprzedzeniem.
- oszczędności: dane dostarczają też producentom informacje, potrzebne do usprawnienia procesów produkcyjnych i zminimalizowania strat. Bez twardych danych trudno jest dokładnie zmierzyć poprawę produkcji i mieć pewność, że zmiany przyniosły firmie realne oszczędności.
Możliwe wyzwania
Internet rzeczy (IoT) oraz jego zastosowanie do dużych zbiorów danych i analiz doprowadziły do powstania nowej generacji produkcji. Obejmuje ona wykorzystanie danych do obniżenia kosztów poprzez planowanie sprzedaży i operacji, radykalnie zwiększoną produktywność, optymalizację łańcucha dostaw i dystrybucji oraz nowe rodzaje usług posprzedażowych. Wiąże się to jednak z wieloma wyzwaniami, którym muszą sprostać firmy, aby prowadzić produkcję opartą na danych. Należą do nich m.in.:
- integracja z innymi systemami — wiele systemów i urządzeń ma problem ze skuteczną integracją i komunikacją między sobą. Mogą one wynikać z oddzielnych systemów operacyjnych w różnych działach czy starszego sprzętu. Dlatego agregowanie danych w różnych systemach może być dużym wyzwaniem i zmniejszać wartość zebranych danych. Problem ten pomagają rozwiązań platformy IoT, która łączy wiele poziomów systemów i udostępniają stary sprzęt online.
- zagrożenia bezpieczeństwa — problem bezpieczeństwa IIoT powstał z dwóch głównych powodów. Po pierwsze, im więcej urządzeń jest podłączonych do sieci, tym większa szansa na tworzenie luk w zabezpieczeniach. Po drugie, wcześniej nie zajmowano się bezpieczeństwem na poziomie komputera, co oznacza, że nie opracowano żadnych standardów ani protokołów, dlatego przedsiębiorstwa produkcyjne powinny również zainwestować w rozwiązania zabezpieczające, ograniczające to ryzyko.
- przechowywanie danych — im więcej urządzeń i systemów jest podłączonych w zakładzie produkcyjnym, tym więcej danych zostanie zgromadzonych. Pozornie jest to duża korzyść, ponieważ użytkownik może uzyskać szeroki wgląd w gromadzone dane. Jednak ich dynamiczny wzrost wymaga też miejsca do ich gromadzenia i przetwarzania, co może być dużym i kosztownym wyzwaniem, szczególnie jeśli użytkownik musi przechowywać dane lokalnie, co przemawia za korzystaniem z chmury obliczeniowej.
- niedokładne lub niekompletne dane — niepełne dane produkcyjne mogą mieć ogromny wpływ na ocenę sytuacji, a w efekcie podejmowanie decyzji, zwłaszcza w przypadku krytycznych projektów, w których dane są podstawą sukcesu. Oznacza to również duże nakłady pracy, stratę czasu i wysiłku po to, by uzupełnić niekompletne zapisy lub upewnić się, że są one autentyczne i zgodne ze stanem faktycznym.
Wykorzystaj potencjał danych
Aby czerpać korzyści z optymalizacji procesów produkcyjnych, należy stworzyć strategię opartą na danych, która powinna obejmować trzy podstawowe etapy:
1. Przechwytywanie i monitorowanie danych: gromadzenie danych w czasie rzeczywistym stanowi podstawę efektywnego wykorzystania danych. Umożliwiają to sensory FitMech, zamontowane na maszynach, które mierzą wibracje i przyspieszenia powstające w trakcie pracy, dostarczając informacji na temat efektywności, cykli pracy, przestojów, obłożenia, wydajności czy przerw w pracy w czasie rzeczywistym.
2. Kategoryzacja i wizualizacja danych: zebrane dane muszą zostać przetworzone i przeanalizowane. Dane z sensorów FitMech są następnie przesyłane do chmury obliczeniowej, która przetwarza je, identyfikując status maszyny, cykle pracy czy przestoje. Następnie w panelu administratora oznaczane są przyczyny nieprawidłowości, a w panelu online prezentowane są wyniki analiz danych z czujników w postaci podglądu na żywo i raportów.
3. Analiza i działania biznesowe: zebrane dane prezentowane są w formie przejrzystych raportów, automatycznie dostosowanych do potrzeb różnych modeli monitorowania produkcji. Dzięki temu ułatwiają podejmowanie decyzji i tworzenie strategii. Po zebraniu i przeanalizowaniu danych maszynowych możliwe staje się opracowanie praktycznych strategii optymalizacji wydajności produkcji, a następnie ich wdrożenie.
___
FitMech to firma, która powstała w Poznaniu w 2019 roku jako odpowiedź na brak prostego i łatwego w
montażu systemu do monitorowania produkcji. Jest to pierwszy system dla produkcji przemysłowej,
zaprojektowany z myślą o szybkiej i samodzielnej instalacji, oferowany w formie abonamentu
miesięcznego. Usługa FitMech dostarczana jest wraz z czujnikami, aplikacjami i sztuczną inteligencją.
Dzięki dokładnej analizie pracy maszyn, FitMech pozwala na zwiększenie wydajności procesów
produkcyjnych, identyfikację wąskich gardeł oraz przyczyn przestojów. Dodatkowo, system pozwala
lepiej oszacować czas potrzebny na wykonanie zlecenia produkcyjnego i pokazuje rzeczywistą pracę
maszyny oraz jej możliwości.
Oferowane rozwiązania:
- Czujniki i Monitoring: FitMech dostarcza specjalne czujniki, które można łatwo zamontować na
maszynach produkcyjnych. Te czujniki zbierają dane o pracy maszyn, takie jak prędkość,
temperaturę, wibracje i inne parametry. Wraz z czujnikami dostarczane są aplikacje do
oznaczania przestojów na tablety oraz telewizory (system andon). - Analiza Danych: Dane z czujników są przesyłane do platformy FitMech, gdzie są analizowane
przez sztuczną inteligencję. System identyfikuje wzorce, anomalie i potencjalne problemy w
procesie produkcyjnym. - Optymalizacja Wydajności: FitMech pomaga zwiększyć wydajność produkcji poprzez
optymalizację czasu pracy maszyn. Dzięki analizie danych, system może wskazać, gdzie można
zoptymalizować procesy lub wyeliminować przestoje. - Intuicyjny Interfejs: Platforma FitMech oferuje intuicyjny interfejs użytkownika, który
umożliwia monitorowanie produkcji w czasie rzeczywistym. Użytkownicy mogą śledzić
wydajność maszyn, raporty i analizy. - Bezpieczeństwo i Dostępność: FitMech dba o bezpieczeństwo danych i dostępność swojej
usługi. Dane są szyfrowane, a platforma jest dostępna 24/7.
W skrócie, FitMech to kompleksowe rozwiązanie, które pomaga firmom zwiększyć wydajność produkcji, zoptymalizować procesy i minimalizować przestoje.
W skrócie, FitMech to kompleksowe rozwiązanie, które pomaga firmom zwiększyć wydajność produkcji,
zoptymalizować procesy i minimalizować przestoje
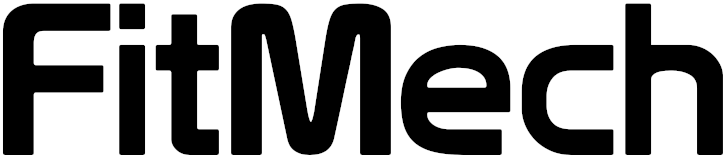